Make4COVID provides crucial PPE to health care workers
Inworks staff adapts tools, enlists volunteers to help frontline workers during COVID-19
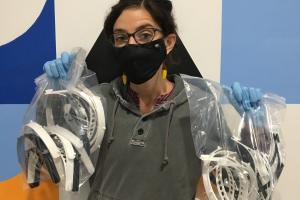
3D printers are being used to create the PPE
At this point, 2,100+ volunteers have registered to help the effort and more than 30,584 face shields have been delivered to dozens of Colorado cities – from Denver to Gunnison to Burlington to Cortez. Plans are underway to send the shields to the Navajo Nation, which has the fifth-highest COVID-19 death rate in the country. Make4Covid has also established collaborations with more than 100 organizations in Colorado and across the country.

Kate Goodman
The face shields comprise a clear curved front piece laser cut by a local company, printed headband pieces are being created by many, many folks with 3D printers, and either elastic or sewn back straps are being sewn by volunteers, she said. The team also creates 3D-printed “ear savers,” a back buckle that allows the health care workers to attach sewn masks to a small plastic strap that the elastic attaches to instead.

More than 30,000 face shields have been distributed.
When FEMA recognized the critical need for PPE, Henderson proposed mobilizing designs that involved printing headbands and laser cutting face shields. He contacted his colleagues and the director at Inworks, Professor Kristin L. Wood, and Make4Covid was soon underway.
“I believed that Coloradans did not want to sit idle while our front-liners were struggling to get the equipment they needed,” Henderson said. “The supply chain disruptions caught us all off guard but we knew that our communities had resources which could rapidly meet some of the need.”
Inworks and the CU Denver College of Engineering, Design and Computing moved to open up university facilities – maintaining social distancing requirements – while community members with expertise were contacted to build a team. At the same time, Karsten Bartels, an anesthesiologist at the CU Anschutz Medical Campus, reached out to strangers who he thought may be able to assist. Several people took the call – from CU Boulder, Red Rocks Community College, and representatives from the biomedical industry, Goodman said. All remain at the core of the movement.

Andrew Henderson
He said the team worked directly with doctors and nurses to improve designs and ensure what they made best fit their needs. They received support and expertise every step of the way, including from CU Anschutz scientists Jeff Kieft and Olivia Rissland, who established protocols for handling and disinfecting of materials in the supply chain; Jennifer Wagner's testing facilities in Bioengineering, which provided rapid access and quantitative metrics to improve designs; and Tom Yeh, faculty at CU Boulder, who provided rapid creation of IT infrastructure that supported the whole effort.
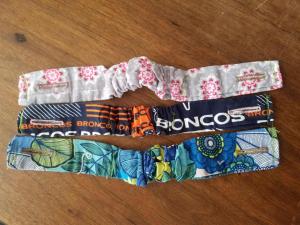
Samples of the back straps
Not only did the group pull together quickly, it has gotten the goods into the community at record speed. Having been hit hard by COVID-19 early on, Gunnison had imposed some of the tightest travel restrictions, blocking all road access during the pandemic. Twelve hours after interfacing with the community, CU Denver and Make4Covid mobilized to send a flight loaded with 220 face shields and other supplies to Gunnison. A subsequent shipment of 250 face shields was sent a few days later, followed by 1,000 additional clear-sheet components to give the community ongoing security for operations, organizers said.
“The caliber of our volunteers is astounding,” Henderson said. “People with decades of experience from medicine and engineering to manufacturing and logistics to fundraising and media – you name it – were willing to jump in and dedicate a lot of time to the pressing issue at hand. In a time when there is so much pain and uncertainty, our actions speak volumes to the solidarity, character and strength of Colorado.”Goodman credits the team and the phenomenal volunteers for the continued outpouring of care.
“From the individual sewing or 3D printing at home, to the large labs humming with dozens of 3D printers and the networks of designers working to provide more design we can produce, we appreciate every single one of you,” Goodman said. “We are ‘many-facturing’ to cover what Colorado needs, and I’m so humbled to be part of this effort. They have cobbled together a supply chain that reaches all over the state, and they should be proud of every piece of equipment we deliver.
She stressed, “When Colorado invests in its universities, the investment pays off in unexpected ways.”